Generators
In the generators section of the equipment library, power generation library members can be viewed, modified, or created for use in a TRACE™ 3D Plus project file. There are five types of generator categories in this library; Combustion Turbine, Internal Combustion Engine, Photovoltaic (Equivalent One Diode), Photovoltaic (Simple), and Wind.
|
Note: Standard TRACE library members cannot be modified or deleted but they can be copied and edited.
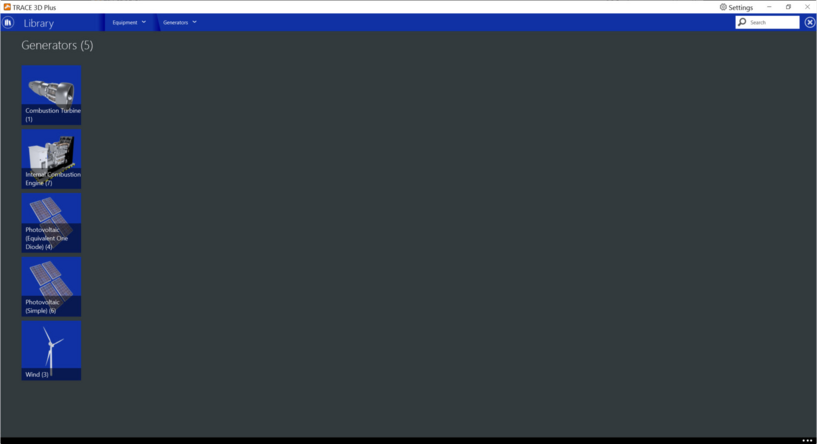